“We want to be ahead of the market”
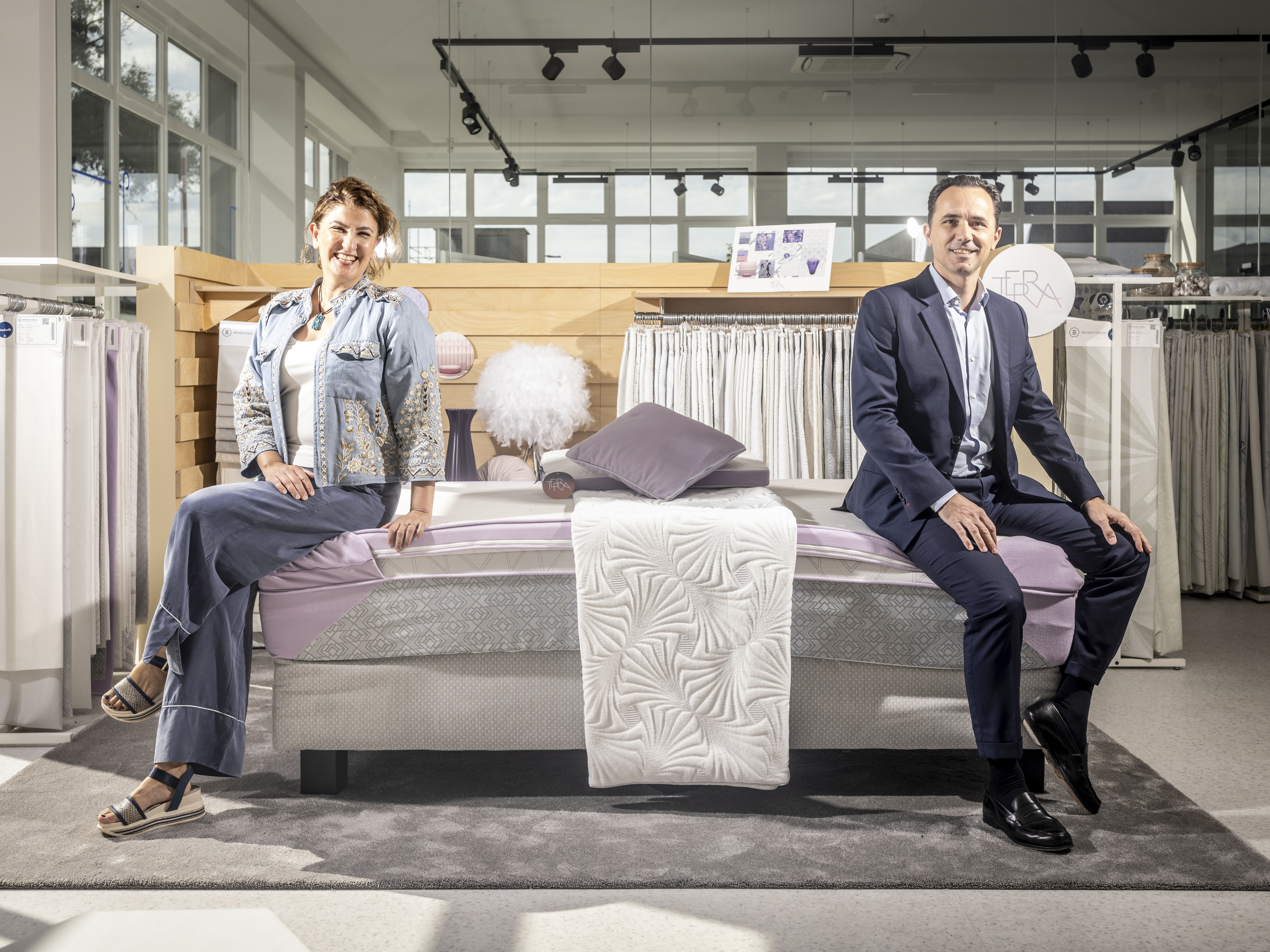
West Flanders-based BekaertDeslee won six awards this year for the quality of its products and its efforts to make mattresses more sustainable. But is the mattress industry ready for more recycling and circularity?
SARAH VANDOORNE, PHOTOGRAPHY FRANKY VERDICKT
On an industrial site on the outskirts of Waregem, CEO Frédéric Beucher and EVP & CMO Demet Tunç welcome us to a showroom full of mattresses. BekaertDeslee does not make and sell those mattresses themselves. Founded in 1892, the company has been a global leader in mattress textiles, from mattress protectors to high-tech covers, for many years. Every day, 110,000 mattresses with textiles from the West Flanders company pass over the counter. It works almost exclusively business-to-business, yet BekaertDeslee feels very involved with the end customer. That has to do with the end goal of its products: a good night's sleep. "It could hardly be more personal," Beucher says in flawless English. English - and Spanish - are the most widely spoken two languages in the company. "And I think Turkish is the third language," Tunç believes. "It shows how international we are. Our roots are in Waregem, but we operate in 18 countries."
Close To You. Tunç repeats that marketing slogan throughout the conversation. "It makes no sense to transport products from one side of the world to the other, when every country has a different preference for mattresses," Beucher adds. "French prefer latex, British want pocket springs. In Belgium, the preference is for a mix of springs and foam. That's why we produce as close as possible to our customers. Belgian mattress manufacturers know that our textiles come from Europe, for example from the Czech Republic or Spain. But Argentinian customers don't have to look that far. That wouldn't exactly be ecological."

“It makes no sense to transport products from one side of the world to the other, when each country has a different preference for mattresses” - Frédéric Beucher, BekaertDeslee
Main Prize
BekaertDeslee was a winner at this year's sector trade fair Interzum. It was the first time that a company went home with six awards, including the top prize: the 'Best of the Best'. All categories had a link to sustainability and quality, Tunç stressed. The fabrics in the showroom refer to the company's sustainable ambition. Recycling and circularity are words that keep coming back. BekaertDeslee recycles production waste as raw material. SmartSleeve, the product that won the Best of the Best Award, is 100 percent recyclable and includes recycled plastic. The prize beast also contains a QR code so that consumers and the recycling company can find out which substances the textile contains. This puts BekaertDeslee ahead of the European eco-design legislation recently adopted by the European Parliament, which requires every product to have a digital passport to ensure a longer life.
Recycled or not, most of BekaertDeslee's products are made of polyester, a fossil fuel-based fabric. This is not ideal, Beucher realizes. He compares it to an electric car: the raw materials we need for those batteries are also polluting, yet it is a better solution than the previous generation of cars. In the course of that transition, other - and better - innovations will follow. "We cannot know what sustainable solutions will be available in five years, but we are anticipating them. We want to be ahead of the market," Beucher says. "And if you compare it to the footprint of cotton, polyester is the best choice for us right now. Worldwide, 80 million tons of polyester are used. We don't have enough land to harvest that much cotton. And polyester is easier to recycle and keep recycling." This is confirmed by the Centexbel research institute, although textile consultant Edwin Maes notes that it involves energy-intensive chemical recycling. "Moreover, more research is needed to be sure that the quality will remain the same," Maes said.
Alternative to PFAS
Another thorny issue is fabric finishing. As a manufacturer, you don't want end customers to accidentally set their mattress on fire. In the realm of fire-resistant and water-repellent chemicals, the industry has used the forever chemicals PFAS for years. "Only recently a scandal broke out about how harmful they are, while we have been looking for alternatives behind the scenes for some time. Today we can completely replace PFAS with a fluorine-free alternative, at about the same cost," Tunç says. To be ahead of the market. "In this sector there is a lot of copy-pasting," Tunç continues. "Often, however, we are the first, or we try to be. Our research and development departments are immense, we work closely with both our suppliers and innovative start-ups. Innovation takes a long time, sometimes five years or more. We work on all kinds of tracks and can't get out there quickly."
Designed for disassembly
However, the real challenge to making mattresses more sustainable is not the fabrics, but what happens to the mattress after use. "Our share in a mattress is very small," says Tunç. BekaertDeslee has no control over the final destination, because that responsibility lies with the mattress manufacturers. Many companies suggest taking back an old mattress when the end customer orders a new one. "But do you know what happens to it then? Most mattresses just get burned." This is precisely why BekaertDeslee is betting on circular design. So, it joined forces with Resortecs, a Belgian innovation that develops sewing thread that can melt, to promote recycling. Mattress covers without zippers are another example of designed-for-disassembly. Both innovations received an Interzum Award. "This allows the textiles to last longer, even if the mattress is depreciated," he says. Which brings us to a final tricky point: the lifespan of mattresses. "It is generally believed that it is best to replace your mattress every five to 10 years," Tunç knows. Although she knows plenty of people who do as much as twenty years with the same mattress. Not a good idea, she thinks. "The problem is not the fabric, but the mattress core. The memory foam or latex in it cannot last twenty years."

'We cannot know what sustainable solutions will be available five years from now, but we are anticipating them' - Frédéric Beucher, BekaertDeslee
MATTRESSES ARE INCREASINGLY BEING RECYCLED
Although discarded mattresses are usually incinerated, according to BekaertDeslee, an industry survey shows that mattresses are increasingly getting a second life. The waste processing company Renewi recycles 1.5 million mattresses a year in Belgium and the Netherlands. Research projects are underway with BekaertDeslee and others, and Renewi is also working with IKEA. Recycling a mattress is not yet 100 percent successful, admits innovation manager Philip Heylen. "We hit up to 90 percent. We take out metal springs, from plastics we can recycle polyutherane mechanically and polyols go through a chemical recycling process. The textiles go to specialists like the Dutch textile company Wolkat. The biggest challenge is the memory foam." On the site of waste processor Vanheede Environment Group, one of Renewi's suppliers (and competitors), we see many such foam mattresses. Their processing method could be described as "incineration," but Vanheede also prides itself on always being able to do something with old mattresses. "The material only comes to us when no one else has found a recycling solution for it," says sales manager Nico Kimpe. He shows the end product of the "incineration": a glass bowl with wads of material made from mattresses. The waste stream can be converted into a kind of 'biological coal,' an alternative fuel and raw material for the metal industry, among others. In this way, Vanheede is working with ArcelorMittal to make metal production more sustainable.